Professional Premium Aluminum Oxide Products Supplier
PRODUCT PARAMETERS
Description
Overview of Alumina Bar
An alumina bar is a ceramic bar made from aluminum oxide (Al₂O₃), commonly referred to as alumina. It is a high-performance material known for its excellent thermal and electrical insulating properties, mechanical strength, and resistance to wear and corrosion. Alumina bars are widely used in industries where durability and resistance to harsh environments are essential.
Alumina is available in different grades depending on the purity and the specific application requirements. The most common grades are 99.5% alumina and 95% alumina, with higher purity versions providing better electrical insulation and higher strength.
Features of Alumina Bar
- High Hardness: Alumina bars are extremely hard and are often used in applications where wear resistance is crucial, such as in mechanical components or abrasive environments.
- High Thermal Conductivity: Alumina has excellent heat dissipation properties, making it ideal for applications involving high temperatures.
- Electrical Insulation: Alumina bars are excellent electrical insulators, with high dielectric strength. This makes them useful in electrical and electronic applications.
- Corrosion Resistance: Alumina is highly resistant to corrosion, even in acidic or basic environments. It maintains its integrity in harsh chemical surroundings.
- Wear Resistance: Due to its hardness and stability, alumina is resistant to abrasion, making alumina bars suitable for high-friction applications.
- High Purity: Higher-purity alumina bars (e.g., 99.5%) are used for more specialized applications that require superior performance.
- Excellent Mechanical Properties: Alumina bars exhibit good compressive strength, high tensile strength, and can withstand considerable mechanical stress.
Specifications of Alumina Bar
Specification | Description |
Material | Aluminum Oxide (Al₂O₃) |
Purity | 95% to 99.5% |
Density | 3.6 to 3.9 g/cm³ |
Hardness | Mohs hardness: 9 (Very hard, almost as hard as sapphire) |
Compressive Strength | 1500–2200 MPa |
Tensile Strength | 200–350 MPa |
Flexural Strength | 200–400 MPa |
Thermal Conductivity | 25–30 W/m·K (varies with purity) |
Thermal Expansion | 7–8 x 10⁻⁶ /°C |
Dielectric Strength | 20–30 kV/mm (Excellent electrical insulator) |
Maximum Operating Temperature | Up to 1800°C (3272°F) |
Color | White, can be slightly off-white or cream depending on the purity and processing |
Machining | Difficult to machine (requires diamond tools or specialized equipment) |
Electrical Resistivity | Very high (Excellent insulating properties, ideal for use in electrical applications) |
Corrosion Resistance | Excellent, resistant to acids, bases, and most chemicals |
Wear Resistance | Very high, making it suitable for abrasive environments |
Form | Bars, rods, tubes, custom shapes |
Size Range | Typically 2–50 mm in diameter, length from 50 mm to several meters, depending on application |
Manufacturing Process | Extrusion, pressing, casting, sintering at high temperatures |
Common Grades | 95% Alumina, 99.5% Alumina (higher purity available for specialized applications) |
Applications | Electrical insulators, wear parts, substrates for electronic components, thermal management, etc. |
Applications of Alumina Bar
- Electrical & Electronics:
- Insulators: Used as electrical insulators in high-voltage electrical components, such as capacitors, resistors, and insulator rods.
- Substrates for Electronics: Alumina bars serve as substrates for electronic devices, particularly in microelectronics and circuit boards.
- Aerospace & Automotive:
- Thermal Management: Alumina bars are used in aerospace and automotive industries to manage heat dissipation in engines, turbines, and other components.
- Wear-resistant Components: Used for producing high-durability components in engines, transmissions, and suspension systems.
- Mining & Material Handling:
- Lining Material: Due to its high resistance to wear and corrosion, alumina is often used as a lining material in mining equipment, chutes, and hoppers.
- Ceramics & Wear Parts:
- Machine Components: Alumina bars are used in industrial machinery, such as pumps, valves, and mechanical seals, where abrasion resistance and durability are required.
- Medical:
- Dental Applications: Used in prosthetics and dental implants due to its biocompatibility and durability.
- Medical Devices: Alumina is also used in high-performance medical devices such as surgical tools and diagnostic instruments.
- Coatings & Abrasives:
- Coatings: Alumina is used as a coating material in situations requiring protection from wear, heat, or chemical corrosion.
- Abrasives: It is used in the production of abrasive materials for polishing, grinding, and cutting applications.
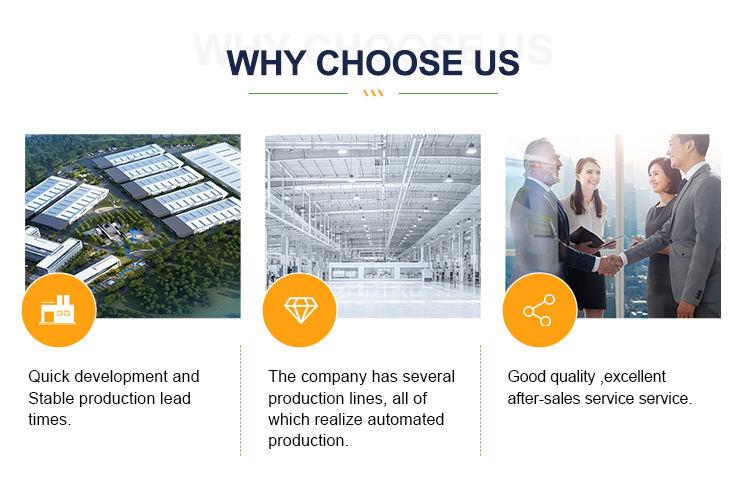
Company Profile
Alumina Technology Co., Ltd.! We focus on the research and development, production and sales of alumina products, serving the electronics, ceramics, chemical and other industries. Since its establishment in 2005, the company has been committed to providing customers with the best products and services, and has become a leader in the industry through continuous technological innovation and strict quality management.
Our products includes but not limited to Alumina Boat, Alumina Crucible, Alumina Dish, Alumina Foam Filter, Alumina Plate, Alumina Rod, Alumina Bar, Alumina Balls, Filter Alumina, Nano Alumina Powder, Spherical Alumina Powder, ect. please feel free to contact us.(nanotrun@yahoo.com)
Payment Methods
T/T, Western Union, Paypal, Credit Card etc.
Shipment Methods
By air, by sea, by express, as customers request.
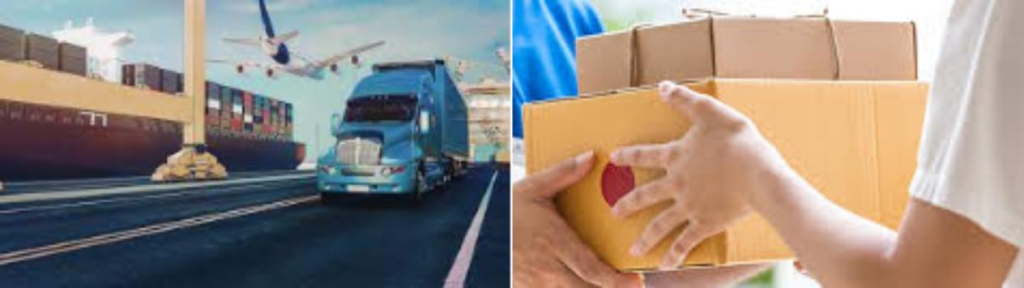
FAQs of Alumina Bar
1. What is an alumina bar?
An alumina bar is a ceramic bar made from aluminum oxide (Al₂O₃). It is known for its high strength, hardness, thermal conductivity, electrical insulating properties, and resistance to corrosion and wear.
2. What are the benefits of using alumina bars?
Alumina bars offer numerous advantages, including excellent wear resistance, high mechanical strength, superior thermal conductivity, and excellent electrical insulation. They are also highly resistant to corrosion and can withstand high temperatures.
3. What are the common grades of alumina?
The most common grades are:
- 99.5% Alumina: High purity, suitable for demanding electrical, mechanical, and thermal applications.
- 95% Alumina: Slightly lower purity, but still effective for many industrial uses where a balance between cost and performance is necessary.
4. What industries use alumina bars?
Alumina bars are widely used in industries such as electronics, aerospace, automotive, mining, medical, and manufacturing. They serve as electrical insulators, wear-resistant components, thermal management devices, and abrasive tools.
5. Can alumina bars be used in high-temperature environments?
Yes, alumina bars can withstand very high temperatures, typically up to 1800°C (3272°F), making them ideal for use in high-temperature applications such as furnaces, kilns, and aerospace components.
6. How are alumina bars manufactured?
Alumina bars are typically manufactured through ceramic processing techniques such as extrusion, pressing, or casting. The material is shaped and then fired in a kiln at high temperatures to achieve its final properties.
7. What are the main challenges with alumina bars?
While alumina bars have many benefits, they are relatively brittle compared to metals, so they can fracture under impact or shock. Additionally, they can be difficult to machine due to their hardness, requiring specialized equipment.
8. Are alumina bars environmentally friendly?
Yes, alumina is an environmentally friendly material. It is non-toxic, and alumina can be recycled and reused, making it a sustainable choice for various industrial applications.