Professional Premium Aluminum Oxide Products Supplier
PRODUCT PARAMETERS
Description
Overview of Alumina Ceramic Balls
High alumina ceramic balls, also known as ceramic alumina balls, are high-performance materials primarily composed of aluminum oxide (Al₂O₃). With alumina content ranging from 92% to 99.5%, these ceramic balls are renowned for their excellent hardness, wear resistance, and thermal stability. They are widely used in a variety of industries, including grinding, milling, chemical processing, and petrochemical applications. High alumina balls offer exceptional resistance to abrasion and corrosion, making them the ideal solution for high-demand applications requiring superior durability and longevity.
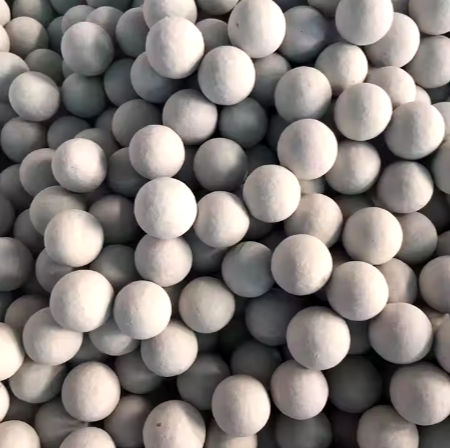
Alumina Balls
Features of Alumina Ceramic Balls
- High Hardness: Rated at 9 on the Mohs scale, these balls provide excellent abrasion resistance, making them ideal for grinding and milling applications.
- Thermal Stability: Capable of withstanding temperatures up to 1700°C, high alumina balls are suitable for high-temperature processing environments.
- Excellent Wear Resistance: Due to their hardness and low wear rates, these ceramic balls last longer than other types of grinding media, reducing maintenance costs and downtime.
- Corrosion Resistance: They are highly resistant to a wide range of acids, alkalis, and other corrosive substances, making them suitable for harsh chemical environments.
- Low Porosity: Their low porosity minimizes water absorption, ensuring consistent performance in moist environments.
- Chemical Inertness: These ceramic balls are chemically inert, providing stability in sensitive processes like catalytic reactions.
- Customization: Available in various sizes (from 0.5 mm to 50 mm) and shapes (spherical, cylindrical, etc.) to meet specific industry requirements.
Specification of Alumina Ceramic Balls
Property | Specification |
Primary Material | Aluminum Oxide (Al₂O₃) |
Alumina Content | 92%, 95%, 99%, or 99.5% |
Other Components | Small amounts of silica (SiO₂), iron oxide (Fe₂O₃) |
Density | 3.50 g/cm³ to 3.90 g/cm³ (depending on grade) |
Hardness | 9 on Mohs scale (high hardness) |
Bulk Density | 2.7–3.7 g/cm³ |
Water Absorption | <0.01% |
Compressive Strength | >2500 MPa |
Tensile Strength | 150–250 MPa |
Modulus of Elasticity | 300–350 GPa |
Fracture Toughness | 3–4 MPa·m^1/2 |
Thermal Conductivity | 20–30 W/m·K |
Coefficient of Thermal Expansion (CTE) | 7–8 x 10⁻⁶/°C |
Maximum Service Temperature | Up to 1700°C (higher for 99% alumina) |
Size Range | 0.5 mm to 50 mm (commonly 1 mm to 30 mm) |
Shape | Spheres, cylinders, or custom shapes |
Tolerance | ±0.1 mm to ±0.5 mm |
Acid and Alkali Resistance | Excellent resistance to acids and alkalis |
Oxidation Resistance | High resistance to oxidation at elevated temperatures |
Applications | Grinding media, catalyst support, insulation, milling, chemical and pharmaceutical industries |
Packaging | Bulk, drums, or bags (typically 25 kg or 50 kg) |
Storage | Dry, cool place to avoid moisture exposure |
Applications of Alumina Ceramic Balls
- Grinding & Milling: Commonly used as grinding media in ball mills and other grinding machines to process materials like minerals, pigments, chemicals, and pharmaceuticals. Their high hardness and low wear rates help achieve finer grinding with minimal contamination.
- Catalyst Support: In petrochemical and chemical industries, these ceramic balls serve as catalyst support media. Their high surface area and resistance to extreme conditions make them ideal for supporting catalysts in chemical reactions, such as in refining processes and petrochemical production.
- Heat-Resistant Insulation: Due to their high-temperature resistance, high alumina balls are used in industries that require high-performance insulation materials, such as in furnaces and reactors.
- Ceramic and Glass Manufacturing: Used as grinding and polishing media in the production of ceramics and glass, where maintaining surface finish quality and consistency is critical.
- Water Treatment & Filtration: Used in water filtration systems as support for catalytic filtration processes or for mechanical filtration due to their uniform size and chemical stability.
- Chemical & Pharmaceutical Industry: In chemical reactors, high alumina balls are employed for their ability to resist corrosive chemicals and high temperatures, often acting as support structures in various types of chemical processes.
- Abrasives & Polishing: These ceramic balls are used in abrasive and polishing applications due to their hardness and smooth surface finish, perfect for polishing delicate or sensitive materials.
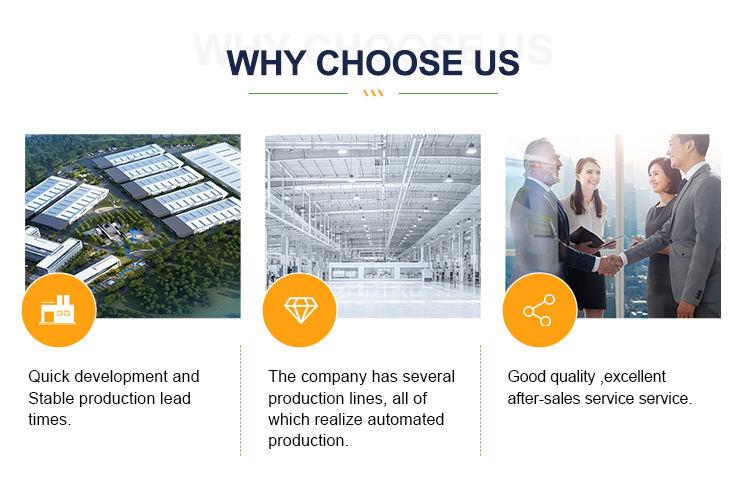
Company Profile
Alumina Technology Co., Ltd.! We focus on the research and development, production and sales of alumina products, serving the electronics, ceramics, chemical and other industries. Since its establishment in 2005, the company has been committed to providing customers with the best products and services, and has become a leader in the industry through continuous technological innovation and strict quality management.
Our products includes but not limited to Alumina Boat, Alumina Crucible, Alumina Dish, Alumina Foam Filter, Alumina Plate, Alumina Rod, Alumina Bar, Alumina Balls, Filter Alumina, Nano Alumina Powder, Spherical Alumina Powder, ect. please feel free to contact us.(nanotrun@yahoo.com)
Payment Methods
T/T, Western Union, Paypal, Credit Card etc.
Shipment Methods
By air, by sea, by express, as customers request.
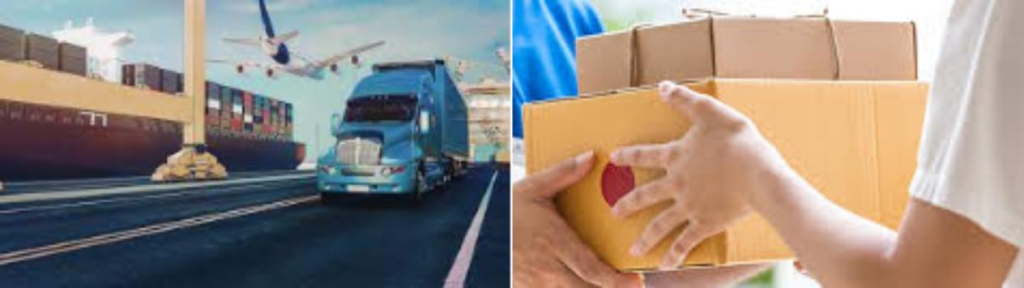
FAQs about Alumina Ceramic Balls
1. What are high alumina ceramic balls made of?
- High alumina ceramic balls are primarily composed of aluminum oxide (Al₂O₃), with varying alumina content (92%, 95%, 99%, or 99.5%) depending on the grade and application.
2. What are the key benefits of using high alumina ceramic balls in grinding?
- The primary benefits include high hardness (9 on Mohs scale), excellent wear resistance, long lifespan, low water absorption, and high chemical and thermal stability. These features make them ideal for grinding hard materials with minimal contamination and maintenance.
3. What industries use high alumina ceramic balls?
- High alumina balls are used in a variety of industries, including mining, cement, ceramics, petrochemicals, pharmaceuticals, chemicals, and water treatment. They are commonly found in applications like grinding, catalyst support, high-temperature insulation, and polishing.
4. How do high alumina balls compare to other grinding media?
- Compared to traditional grinding media such as steel balls, high alumina balls have a higher hardness, lower wear rate, and better corrosion and chemical resistance, which makes them more durable and effective for certain grinding and milling processes, especially in sensitive or aggressive environments.
5. Are high alumina ceramic balls resistant to heat?
- Yes, high alumina ceramic balls are highly resistant to heat and can withstand temperatures up to 1700°C (depending on the alumina content). This makes them suitable for high-temperature applications in industries like ceramics, metallurgy, and chemical processing.
6. How are high alumina balls used as catalyst support media?
- In catalytic processes, high alumina ceramic balls serve as support structures for catalysts in chemical reactors. Their high surface area, stability, and resistance to high temperatures make them ideal for supporting catalytic materials that facilitate chemical reactions.
7. What sizes do high alumina ceramic balls come in?
- High alumina ceramic balls are available in a range of sizes, from 0.5 mm to 50 mm in diameter, with spherical being the most common shape. They can also be customized for specific industrial applications.
8. How should high alumina ceramic balls be stored?
- High alumina balls should be stored in a dry, cool environment, away from moisture, to prevent any potential damage or degradation. Proper storage ensures their longevity and performance.