Professional Premium Aluminum Oxide Products Supplier
Alumina Foam Filter
A Brief Overview of Alumina Ceramic Foam Filter
Alumina Ceramic Foam Filter is a porous material made of high-purity alumina (Al₂O₃), which has a three-dimensionally connected pore structure, similar to foam. This unique structure gives it excellent fluid passage performance and particle interception capability. In metal casting, melt treatment and other high-temperature processes, this filter effectively removes inclusions from the melt and improves product quality. Due to its excellent heat resistance and chemical stability, it can maintain stable operation even under extreme conditions. In addition, its high mechanical strength allows it to withstand large pressure differences without deformation or rupture. Therefore, alumina ceramic foam filter is one of the indispensable key components in modern industrial production.
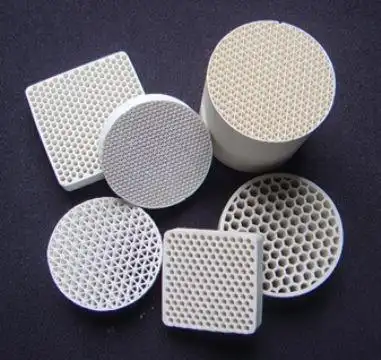
Advantageous features of alumina ceramic foam filter
Alumina ceramic foam filter is ideal for many industrial applications with its unique advantages. Firstly, it possesses extremely high heat resistance and can be used continuously at high temperatures of more than 1600°C, which ensures the safety of the molten metal purification process. Secondly, the alumina ceramic foam filter is chemically inert and will not react with any molten metal or non-metallic material, ensuring product purity. Further, its porous structure provides highly efficient filtration that effectively traps tiny particles of impurities while allowing for smooth liquid flow and reduced pressure drop. Additionally, the product offers a long service life, as it is not easily worn or corroded due to its high hardness and abrasion resistance. Finally, the aluminum oxide ceramic foam filter is easy to install and replace, bringing great convenience and economy to users.
Specifications Table for Alumina Ceramic Foam Filters
Parameter | Specification |
---|---|
Material Composition | High-purity alumina (Al₂O₃) |
Purity Level | ≥99.7% |
Operating Temperature | Up to 1600°C |
Chemical Resistance | Excellent, inert to most molten metals and chemicals |
Porosity | Typically 40-80% |
Average Pore Size | Ranges from 5 PPI (pores per inch) to 60 PPI |
Mechanical Strength | High, suitable for high-pressure applications |
Dimensional Stability | High |
Surface Finish | Smooth or as specified |
Standard Sizes | Various sizes available, custom options possible |
Color | White or off-white |
Packaging | Individually wrapped, quantity packed |
Manufacturing Process of Alumina Ceramic Foam Filter
The manufacturing of alumina ceramic foam filters is a complex and precise process, from the selection of raw materials to the quality control of the final product, each link is crucial. First is the raw material preparation stage, which requires the selection of high-purity alumina powder, and possibly the addition of appropriate amounts of binder and other auxiliary components to optimize the molding properties. Next is the foam generation process, where a blank with a three-dimensional connected pore structure is prepared, usually by foaming or template replication. A drying process is then performed to remove moisture from the body of the blank for subsequent sintering. Sintering is a critical step carried out in a strictly controlled high-temperature environment to densify the material and obtain the final physical and chemical properties. Afterwards, the sintered filters are subjected to surface treatments, such as grinding and polishing, as required to enhance the quality of appearance and functional properties. Finally, all products undergo rigorous inspection, including dimensional accuracy, porosity testing as well as heat resistance and chemical stability testing, and only products that meet the standards are placed on the market.
Application areas of alumina ceramic foam filters
Alumina ceramic foam filters play an important role in several industries due to their excellent performance. In the metal casting industry, they are widely used in the melting process of aluminum alloys, magnesium alloys, copper alloys and other non-ferrous metals and their alloys for removing solid impurities in the melt, thus improving the quality of castings. In the glass manufacturing industry, these filters also play an important role in removing air bubbles and tiny particles from the glass melt, ensuring clarity and smoothness of the final product. In addition, alumina ceramic foam filters are also used in the chemical industry as highly efficient separators of gaseous or liquid media, for example to remove harmful particles in exhaust gas treatment systems. In the electronics industry, they can also be used as insulating supports or heat dissipation elements in high-temperature environments. In short, alumina ceramic foam filters have become an indispensable part of many industrial sectors due to their versatility and reliability.
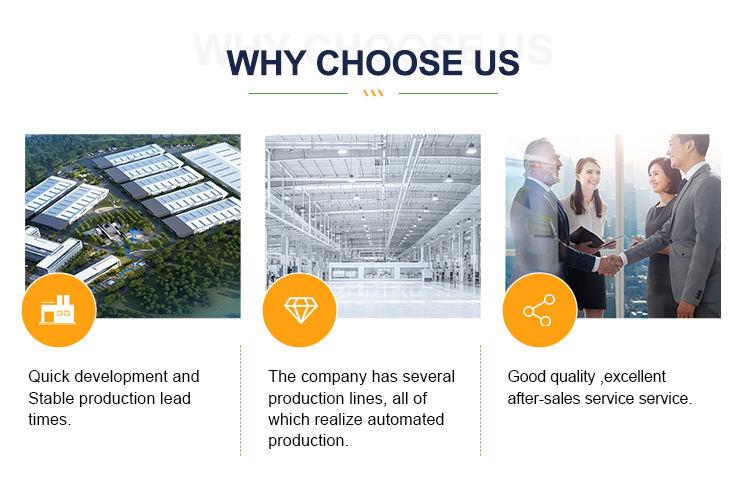
Company Profile
Alumina Technology Co., Ltd.! We focus on the research and development, production and sales of alumina products, serving the electronics, ceramics, chemical and other industries. Since its establishment in 2005, the company has been committed to providing customers with the best products and services, and has become a leader in the industry through continuous technological innovation and strict quality management.
Our products includes but not limited to Alumina Boat, Alumina Crucible, Alumina Dish, Alumina Foam Filter, Alumina Plate, Alumina Rod, Alumina Bar, Alumina Balls, Filter Alumina, Nano Alumina Powder, Spherical Alumina Powder, ect. please feel free to contact us.(nanotrun@yahoo.com)
Payment Methods
T/T, Western Union, Paypal, Credit Card etc.
Shipment Methods
By air, by sea, by express, as customers request.
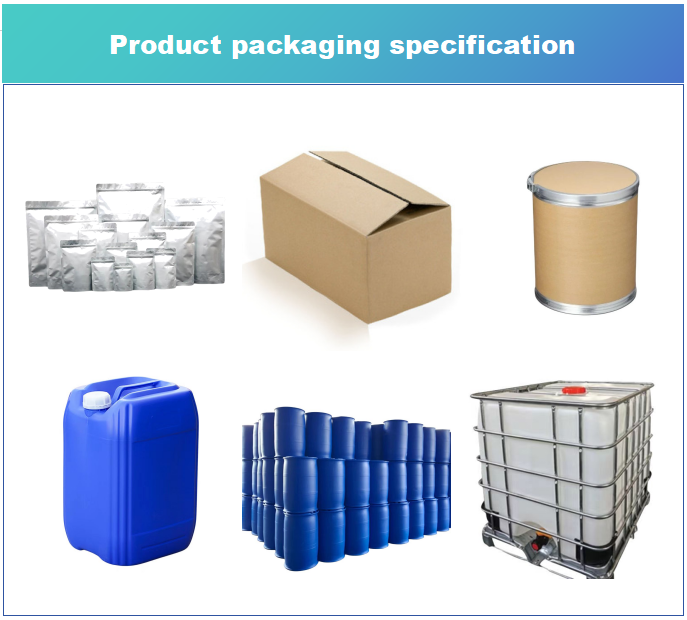
5 FAQs for Alumina Ceramic Foam Filter
Q: What types of particles can the Alumina Ceramic Foam Filter filter filter?
A: It can effectively filter oxides, carbides, and other non-metallic inclusions in molten metals, glass melts, or other high-temperature fluids, with particle sizes generally ranging from tens of microns to hundreds of microns.
Q: How to choose the right specification of alumina ceramic foam filter?
A: Factors such as melt type, flow requirements, required filtration accuracy, and operating temperature should be considered when selecting to determine the most suitable porosity and size specifications.
Q: Does alumina ceramic foam filter need pretreatment?
A: Usually no special pretreatment is required, but in order to ensure the best filtration effect, it is recommended to carry out simple cleaning and drying treatment before the first use.
Q: How long is the service life of alumina ceramic foam filters?
A: The service life depends on the specific application conditions, but under normal maintenance, a high quality alumina ceramic foam filter can be used for multiple melt cycles.
Q: What should I do if I find a broken alumina ceramic foam filter?
A: Once breakage occurs, the filter should be stopped immediately and replaced with a new one to avoid affecting the filtration efficiency or causing safety hazards.